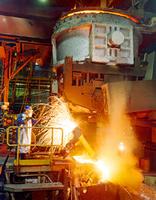
Le fer est la principale matière première utilisée dans la production de l’acier qui est lui-même un alliage de fer concentré avec une faible quantité de carbone. Au total, la production d’acier engendre 98 % de la production de fer tandis que le 2 % restant va à l’électronique et à des fins non métallurgiques. Historiquement, l’extraction du fer et la production d’acier ont constitué des industries majeures au Canada, surtout dans les zones industrielles de l’Ontario et du Québec.
Minerai de fer
Après l'oxygène, le silicium et l'aluminium, le fer est le quatrième élément dont regorge la croûte terrestre. On le trouve dans certains minerais, les plus importants étant la magnétite, l'hématite, la goethite, la pyrrhotine, la sidérite, l'ilménite et la pyrite. On utilise le terme « minerai de fer » chaque fois que la roche contient suffisamment de minéraux de fer pour rendre son exploitation rentable. Bien qu'abondantes, la pyrite et la pyrrhotite servent rarement de minerais de fer en raison de leur teneur élevée en soufre. Les principaux minerais de fer canadiens sont l'hématite et la magnétite suivies de la sidérite et de l'ilménite. En plus d'oxydes de fer, les minerais de fer contiennent une gangue, des minéraux indésirables lors de l'élaboration du fer comme le quartz et la fluorite.
Les minerais contenant une proportion de fer supérieure à 54 % ou plus sont considérés comme étant de grande qualité tandis que ceux ayant une proportion plus faible doivent être valorisés afin d’être commercialisables au niveau technique comme minerai de fer. On extrait le minerai de fer des roches en enlevant la gangue par concentration. Pour cela, on broie finement le minerai, puis on sépare les particules riches en fer des particules de la gangue (par exemple, par séparation magnétique). La matière riche en fer (le concentré) est agglomérée en plus gros amas avant la fusion en l'assemblant en boulettes (boulettage) ou en chauffant le concentré jusqu'à ce que ses particules se collent ensemble (frittage).
En 2014, le Canada est le huitième producteur mondial de minerai de fer. Le producteur le plus important est la Iron Ore Company of Canada, dont Rio Tinto contrôle la majorité des actions.
La plus grande source g.ologique de fer au Canada est, de loin, la fosse du Labrador, une immense formation qui s’étend du Labrador jusqu’au nord du Québec. Ces deux provinces représentent la quasi-totalité du fer extrait au pays. Découverte en 1892, la fosse est un site d’extraction de fer depuis 1954 et a suscité de plus en plus l’attention du secteur de l’extraction avec l’accroissement de la demande pour cette ressource.
Acier
L'acier est le matériau industriel le plus important du monde avec une production annuelle de 1,5 milliard de tonnes. Sans acier, notre monde n'existerait pas tel qu'il est : des pétroliers aux punaises, des camions aux boîtes en fer blanc, des pylônes aux grille-pain. On en produit énormément, mais heureusement on le recycle facilement. De nombreuses aciéries canadiennes fabriquent de l'acier entièrement avec de la ferraille.
Malgré les formidables réserves de minerai de fer du Canada, l’industrie
Production sidérurgique
La fabrication de fer requiert du minerai de fer, du charbon et de la pierre (calcaire, dolomite). La fabrication d'acier demande du fer, de la ferraille d'acier et du fondant (chaux, pierre à chaux calcinée). On fond le minerai de fer pour produire un métal brut appelé « métal en fusion » quand il est liquide ou « fonte brute » quand il est solide. Le métal en fusion est affiné pour enlever les impuretés et développer la composition désirée. L'acier liquide est coulé en blooms, en brames ou en billettes, puis ces produits semi-finis sont façonnés dans les formes désirées par laminage ou par forgeage.
Composants de l’industrie
La sidérurgie est divisée en quatre secteurs : les sidérurgies intégrées, les aciéries intégrées, l'industrie de transformation d'acier et les fonderies et les fabricants.
Sidérurgies et aciéries intégrées
Les sidérurgies intégrées (basées sur le minerai) sont typiquement de grandes entreprises qui produisent annuellement plus d'un million de tonnes, exploitent des mines de fer et de charbon (souvent en coentreprises) et des aciéries. Parmi les sidérurgies intégrées, citons Essar Steel Algoma (auparavant Aciers Algoma Inc.) de Sault Ste Marie en Ontario, Dofasco Inc. de Hamilton en Ontario et ArcelorMittal Montréal (anciennement Sidbec-Dosco (Ispat) Inc.).
Aciéries intégrées
Les aciéries intégrées dépendent de la ferraille comme source de fer. Elles peuvent fabriquer la même gamme de produits semi-finis (brames, blooms et billettes) et des produits en acier finis comme les sidérurgies intégrées plus grandes (feuillards laminés à chaud, feuillards laminés à froid, tôles, tiges, barres, profilés). Parmi les aciéries intégrées, citons Gerdau-AmeriSteel de Whitby en Ontario et ArcelorMittal de Contrecoeur au Québec.
Les aciéries intégrées sont construites là où l'on peut regrouper économiquement les grandes quantités de matières premières nécessaires. Les plus grandes aciéries canadiennes sont construites le long des Grands Lacs et de la voie maritime du Saint-Laurent, en des endroits où on peut transporter le minerai de fer du Nord de l'Ontario, du Québec, du Labrador, du Minnesota, du Wisconsin et du Michigan et le charbon de la Pennsylvanie, de la Virginie occidentale et du Kentucky. D’autres aciéries intégrées sont cependant construites partout au Canada où l'on trouve de la ferraille en abondance et des débouchés sur place pour les produits en acier finis.
Transformateurs d’acier
Les transformateurs d'acier achètent aux aciéries intégrées des produits d'acier semi-finis et laminés à chaud ou à froid et les transforment pour les revendre aux fabricants qui désirent des quantités d'acier trop petites pour être fournies économiquement par les aciéries intégrées. Les entreprises de recyclage de la ferraille font partie de ce groupe. Parmi les transformateurs, citons les entreprises DJ Galvanizing Corporation de Windsor en Ontario pour la galvanisation par immersion à chaud et Union Drawn Steel de Hamilton en Ontario pour l'étirage de barres.
Fonderies et fabricants
Les fonderies, souvent petites, fabriquent diverses classes de fonte ou d'acier ou les deux. Le métal fondu est coulé à la louche ou versé dans des moules en sable ou en métal. Les pièces coulées peuvent avoir des formes compliquées et sont souvent conçues à l'unité. Les fabricants prennent les divers produits des aciéries et par certaines opérations – coupes à dimension, façonnage, usinage, filetage, poinçonnage, assemblage, revêtement protecteur, etc. – en font une multitude de produits industriels et commerciaux. Parmi les fonderies et les fabricants, citons les entreprises Baycoat Ltd. de Stoney Creek en Ontario pour le revêtement organique et Bombardier Inc. de Valcourt au Québec pour l'estampage et le soudage.
Fabrication du fer
Lorsque le fer devient minerai, le coke et la pierre sont introduits à intervalles réguliers dans le gueulard du haut fourneau. Le coke est le résidu solide partiellement graphité qui subsiste après le retrait des composants volatiles du charbon bitumineux par chauffage dans les fours à coke. Les gaz chauds montent et chauffent ces matières (ils les brûlent), qui descendent lentement dans le puits du four. Le monoxyde de carbone des gaz réagit avec les oxydes de fer dans le minerai pour former du fer métallique et du dioxyde de carbone. Le fer formé fond et, en filtrant à travers la colonne de coke, dissout le carbone. Lorsqu'il atteint le creuset, il est saturé de carbone et contient aussi du silicium, du phosphore, du manganèse et du soufre. La pierre et le minerai forment un laitier liquide qui fond à bas point de fusion, s'écoule librement et absorbe la majeure partie du soufre qui entre dans le four (le coke est la principale source de soufre). Le laitier liquide, composé des minéraux de la gangue et des composants d'oxyde de la pierre, flotte sur le fer liquide et est séparé du métal fondant durant le vidage du haut fourneau. Le coke ne fond pas, il brûle au contact de l'air préchauffé sous pression (soufflage) qui s'infiltre par des tuyères situées juste au-dessus du creuset.
Réduction directe
On transforme le minerai de fer en fer métallique sans fusion, par divers procédés de réduction à l'état solide. Comme il n'y a pas séparation du fer de la gangue dans l'installation de réduction, il faut utiliser des minerais à teneur élevée ou des concentrés (avec plus de 90 % de Fe). Bon nombre de ces procédés à l'état solide utilisent du gaz naturel comme carburant et comme réducteur (monoxyde de carbone et hydrogène). Sidbec-Dosco de Contrecoeur au Québec utilise un tel procédé, appelé Midrex Process.
Le minerai ou les boulettes, ou les deux, à l'état solide, appelées fer réduit direct (FRI), sont fondues dans des fours à arc électrique et transformées en acier de la même façon que la ferraille. La gangue du FRI est enlevée pendant la fabrication de l'acier. Les minéraux de la gangue contenue dans le FRI se combinent avec la chaux ajoutée pour former un laitier fluide. Le FRI est supérieur à la ferraille en pureté et en uniformité de composition, mais ces avantages élèvent le prix.
Fabrication de l'acier
L'acier est un alliage de fer pur et de carbone. Sa teneur en carbone varie d'environ 0,002 % (par exemple, métal pour tôle d'emboutissage) à 1,5 % (par exemple, acier à outils). Les alliages d'acier contiennent d'autres éléments (comme le manganèse, le nickel, le chrome, le vanadium, le molybdène) qui leur donnent une plus grande résistance et des propriétés particulières. L'acier inoxydable par exemple, est un alliage de chrome et de nickel). En plus du carbone, le métal en fusion et la fonte brute peuvent contenir des éléments indésirables comme le silicium, le phosphore et le soufre qu'il faut retirer durant la fabrication de l'acier, car ils rendent l'acier cassant.
Durant la fabrication de l'acier, le métal en fusion ainsi que la ferraille sont introduits dans un récipient à garnissage réfractaire (convertisseur). On injecte alors dans le bain de métal en fusion de l'oxygène et de la chaux dont le mélange produit un laitier qui dissout le soufre et les autres impuretés indésirables sans corroder le garnissage du convertisseur. L'oxygène injecté oxyde le carbone dissous dans le métal en fusion pour former du monoxyde de carbone et produire de la chaleur. Lorsque la teneur en carbone du bain de fusion chute au niveau désiré, on ajoute les éléments d'alliage et l'on verse l'acier liquide dans une poche de coulée préchauffée.
Les producteurs d'acier avec de la ferraille utilisent des fours à arc. La ferraille est chargée dans le four et trois électrodes en graphite descendent de la voûte du four. Des arcs se forment (alimentation à haute tension) lorsque les électrodes s'approchent de la ferraille. Grâce à sa résistance électrique plus élevée et à la chaleur intense rayonnée par les arcs, la ferraille atteint rapidement les températures de fusion.
Affinage de la poche de coulée
L'acier liquide destiné à des usages plus exigeants subit un affinage additionnel dans des unités de traitement de la poche de coulée. Les impuretés restantes, telles que le soufre, l'hydrogène, l'azote et les inclusions non métalliques, sont enlevées. Les méthodes utilisées sont l'agitation à l'argon, la désulfuration à la poudre et le dégazage sous vide.
Coulée continue
Il y a quelques années, la majeure partie de l'acier était coulée en lingots. Les lingots sont de grands blocs rectangulaires d'acier, dont la plupart sont ensuite façonnés en produits semi-finis – blooms, brames, billettes ou formes spéciales – par laminage primaire ou forgeage. Aujourd'hui, la coulée continue (CC) est la principale façon de solidifier l'acier liquide en forme de produits semi-finis. La CC élimine les opérations primaires. Dans une machine CC, l'acier liquide est versé dans un moule en cuivre oscillant refroidi à l'eau, et la brame, le bloom ou la billette sort continuellement du bas. Ces dernières années, le moulage de brame mince a du succès, car il élimine plusieurs étapes de production.
Laminage à chaud et à froid
Des laminoirs réduisent la plupart des brames, des blooms et des billettes en produits laminés à chaud et à froid tels que plaques, tôles en rubans, rails, profilés, barres et fils ronds. Quelques aciers (par exemple, la tôle fine et la tôle en rubans) sont finis par laminage à froid à la température ambiante pour obtenir des tolérances dimensionnelles minimales, un fini de surface de haute qualité et un degré de dureté exact.
Traitement thermique
Il comprend le recuit, la normalisation, la trempe et le revenu. Ces traitements changent les propriétés de l'acier en modifiant sa microstructure cristalline.
Revêtements de protection
L'acier se corrode dans certains environnements. Pour en ralentir l'oxydation (la rouillure), on revêt les produits en acier le plus souvent de zinc, d'étain, tin, d'aluminium, d'émail vitrifié et de revêtements organiques (par exemple, la peinture).
Historique
Au Canada, les Forges Saint-Maurice, près de Trois-Rivières au Québec, produisent du fer à partir de fer terreux et de bogheads locaux pour les besoins des colons et des militaires (voir Ouvrage de forge). La première usine sidérurgique du Haut-Canada, la Marmora Ironworks près de Peterborough en Ontario, commence sa production en 1822. Elle consiste en deux hauts fourneaux (à courant d'air forcé) alimentés en charbon, en une forge à deux ensembles de marteaux hydrauliques et à creusets spéciaux pour produire des barres de fer. Les usines sidérurgiques de Marmora et de Saint-Maurice sont déjà fermées à la fin du XIXe siècle. Elles ne peuvent plus compétitionner avec celles, plus modernes, de l'Ontario et de la Nouvelle-Écosse, qui utilisent des hauts fourneaux chauffés au coke.
Le Canada fabrique ses premiers produits en acier dans les années 1880. Au début du XXe siècle, des aciéries opèrent déjà à Hamilton et à Sault Ste Marie en Ontario et à Sydney en Nouvelle-Écosse. La production de fer et d'acier augmente lentement jusqu'à la Deuxième Guerre mondiale, puis rapidement lorsque l'essor économique d'après-guerre engendre une énorme demande d'acier.
Le procédé Bessemer, inventé en Angleterre en 1856, est le premier procédé de fabrication d'acier à grande échelle. Il est suivi, quelques années plus tard, par l'invention du procédé Martin qui, d'environ 1900 jusqu'au début des années 60, produit le plus d'acier. En 1910, le procédé Bessemer n'est déjà plus utilisé en Amérique du Nord.
Le procédé basique de soufflage d'oxygène au-dessus du bain (BOP) – d'abord connu comme le procédé L.D. (Linz-Donawitz) – provient d'Autriche. Dofosco Inc. introduit le BOP en Amérique du Nord en 1954 et, depuis lors, le procédé Martin décline régulièrement jusqu'à disparaître.
Les Canadiens apportent une contribution notable au progrès de la sidérurgie. Au début des années 60, Air Liquide Canada Ltée conçoit un injecteur qui permet d'introduire de l'oxygène pur à travers le fond des récipients BOP. Cette méthode est développée à l'échelle industrielle en Allemagne en 1968. La première machine de coulée continue d'acier en Amérique du Nord est mise au point en 1954 par Atlas Steel à Welland en Ontario.
En 1959, Stelco Inc. introduit le procédé à bas volume de laitier qui diminue la consommation de coke d'environ 40 %, économisant dans le monde plus de 200 millions de tonnes de charbon par an. Stelco met au point le procédé de refroidissement par barres Stelmor et le Coilbox (boîte à self), un important dispositif d'économie d'énergie utilisé dans les aciéries de feuillards laminés à chaud. Cette entreprise met aussi au point le cycle de recuit court, une autre façon d'économiser l'énergie, universellement adoptée dans la sidérurgie. Stelco met aussi au point la tige torsadée Ardor. Lasco met au point la technique de laminage de refendage, pour faire deux barres avec une seule billette. Ipsco est la première entreprise à installer une tuberie à soudage spiral.
Projet Bessemer Inc., qui est un consortium de sidérurgistes canadiens et du Conseil national de recherches du Canada, a entrepris des recherches en coulée de feuillards à Boucherville, au Québec. Le but ultime de la fabrication d'acier : une seule étape de l'acier liquide au feuillard fini.